Post Date: March 18, 2023
Operational excellence in information technology is a methodology that focuses on continuous improvement and optimization of processes, operations, and technology to deliver value to customers in a way that meets or exceeds expectations.
IT operational excellence is achieved by identifying and mitigating risks ((https://www.ibm.com/cloud/blog/delivering-value-through-operational-excellence#:~:text=Operational%20excellence%20is%20a%20way,and%20employees%20show%20continuous%20improvement.)), streamlining processes, and improving the efficiency of technology systems. This approach is used to improve the effectiveness of IT operations, increase the speed of service delivery, and reduce costs.
Key components of IT operational excellence include process automation, data-driven decision-making, and improved visibility. Companies use a variety of tools and techniques, such as process mining, business process management software, and analytics, to achieve operational excellence.
When implemented well, IT operational excellence can lead to improved customer experience, greater agility and flexibility, and increased efficiency.
Core Principles of Operational Excellence
There are 10 core principles of operational excellence that businesses must adhere to in order to achieve success: create value for the end consumer; work on creating constancy of purpose; maintain humility; respect everyone; think systemically; take steps to maintain quality; maintain the flow of value; do not blame; look for perfection; and make use of scientific thinking.
Operational Excellence Methodologies ((https://www.projectmanager.com/blog/operational-excellence))
Six Sigma: A data-driven approach to improving the quality of products and processes with the goal of reducing errors and defects.
Lean Management: A methodology focused on eliminating waste and reducing cycle time to improve efficiency and quality.
Kaizen: A continuous improvement philosophy that encourages employees to identify, experiment, and implement small steps to continuously improve processes.
Shingo Model: A set of guiding principles and operational strategies that aim to improve the flow of value through an organization.
Operational Excellence Management System: An operational excellence framework developed by Chevron that focuses on managing risks and maintaining safeguards to mitigate those risks.
Implementing Operational Excellence
Organizations must implement a successful operational excellence strategy to restore growth and profitability. This requires leaders to communicate with employees and ask questions, create a plan of action, design a dual operational structure, lead with purpose and compassion, clarify what needs to be done, why it needs to be done, and how it will be done, take small steps to make big changes, and create a fault-tolerant environment.
Effective communication, visibility, and transparency are critical for operational excellence. Leaders should establish an operational excellence group or task force to drive business improvement projects. Additionally, organizations should integrate two parallel operational structures in their organizational architecture, apply digital technologies, and promote collaboration between teams.
Organizations should also adopt the 5S lean principles, create a learning culture of continuous improvement which tolerates mistakes, and reward progress and recognition of achievements. All these steps will help organizations achieve sustainable improvement and operational excellence in the digital age.
Benefits of Operational Excellence
More Productive Employees: Improving operational excellence through effective training and one-on-one coaching can yield a noticeable increase in employee productivity.
Higher Profit Margins & ROI: Achieving operational excellence can result in higher profit margins, allowing businesses to maximize their return on investments.
Streamlined Processes: Operations that are streamlined and efficient can benefit both employees and customers.
Reduced Waste: Applying operational excellence strategies such as Lean Six Sigma can help companies reduce waste and control any associated problems.
More Time for Management: When businesses commit to operational excellence, management has more time to focus on bigger initiatives for company growth.
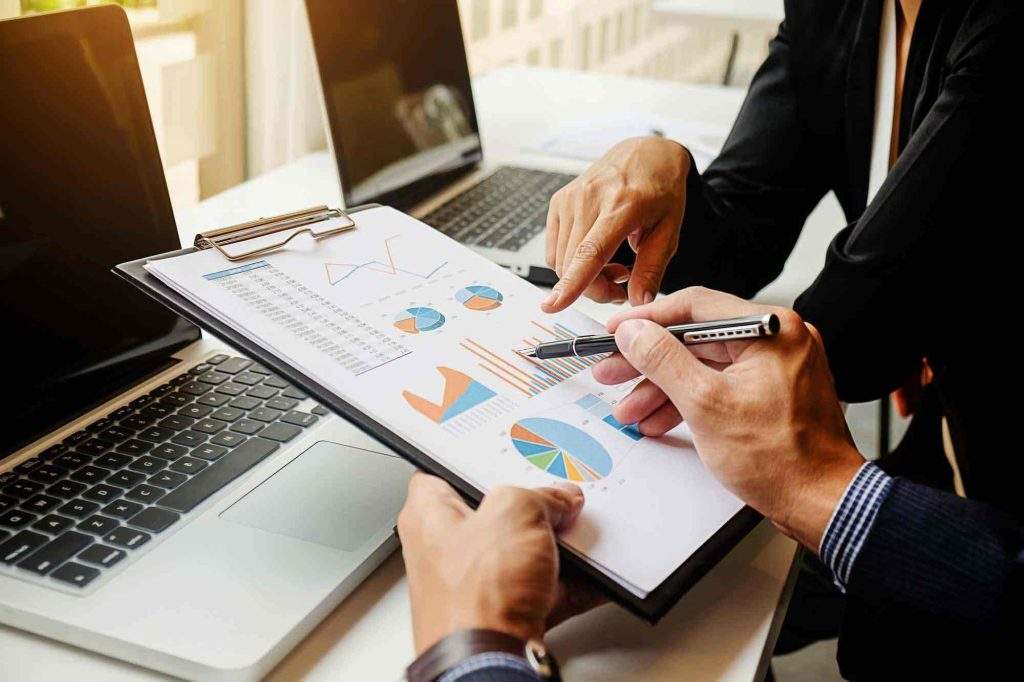
Industries that Use Operational Excellence
Manufacturing: Companies like Motorola and BAE Systems have employed operational excellence methodologies to enhance productivity, decrease downtime and cut out waste.
IT: Using the core principles of operational excellence, IT teams can minimize development rework and improve workflow efficiency in a fast-paced environment.
Healthcare: By focusing on customer experience, operational excellence helps healthcare providers reduce wait times, improve patient portals and better track patient outcomes.
Construction: Implementing operational excellence helps construction companies ensure worker safety, efficient workforce management and cost-effective sourcing of materials.
Retail: Retailers use operational excellence to make sure their stores are running efficiently and that staff are knowledgeable about products and customer service.
Food Services: Operational excellence helps food services improve customer experience, reduce wait times and keep food quality consistent across all locations.
Education: Educational institutions use operational excellence to create an environment where students are engaged and empowered to learn and develop new skills.
Transportation: Operational excellence helps transportation companies improve customer satisfaction, reduce operational costs and ensure safety for passengers and crew.
Operational Excellence Tools
- Value Stream Mapping: This tool is used to depict the flow of a thing being processed and reduce or eliminate the 7 Types of Waste by applying Lean Principles.
- Visual Work Instructions: These are used to train people on a new process and combine words with intuitive pictures.
- Process Analysis Template: This template makes it easy to unhide lean metrics to drive current growth and hide metrics that may be important for the next phase.
- A3 Report: This report tells the story of a process improvement event in an easy-to-follow format on a single sheet of paper.
- Policy Deployment X Matrix: This tool is used to develop and implement strategic plans and unique competitive advantages, benefiting from input and ownership from all levels of the organization.
Conclusion
Operational excellence is a methodology of striving for efficiency throughout an organization’s processes, with the end-goal of ensuring customer expectations are met on an ongoing basis. To achieve operational excellence, organizations must focus on key performance metrics, continuously improve processes, and embrace qualities such as respect for every individual, humility in leadership, and focus on process.
The Shingo Prize recognizes organizations that have achieved operational excellence, and provides an example of the qualities that need to be embraced in order to reach this goal. Organizations must recognize the importance of operational excellence in order to ensure the success of their business.
FAQ About Operational Excellence
Operational excellence is the pursuit of efficiency and effectiveness in business operations. It involves streamlining processes, minimizing waste, and delivering consistent quality. It helps organizations optimize resources, reduce costs, and provide superior value to customers.